Can Magnets Rust?
The effects of rust on magnets and how to prevent it
1. What are neodymium magnets made of?
While you may know the chemical formula of neodymium magnets as NdFeB, or Nd2Fe14B , they are mostly iron and neodymium. By mass, they're roughly two-thirds iron and one-third neodymium. Only a tiny fraction is boron, plus a few other elements.
A raw, unplated magnet is not all that different from a piece of raw iron, at least when it comes to corrosion. Iron rusts in the presence of moisture which is why iron pans are usually kept oiled. Neodymium magnets are like iron; without protection, they rust easily.
To prevent corrosion, most neodymium magnets are plated with a three layer, nickel-copper-nickel plating. This particular plating combination has been the preferred corrosion protection for many years. It performs better than zinc plating or other solutions in most applications.
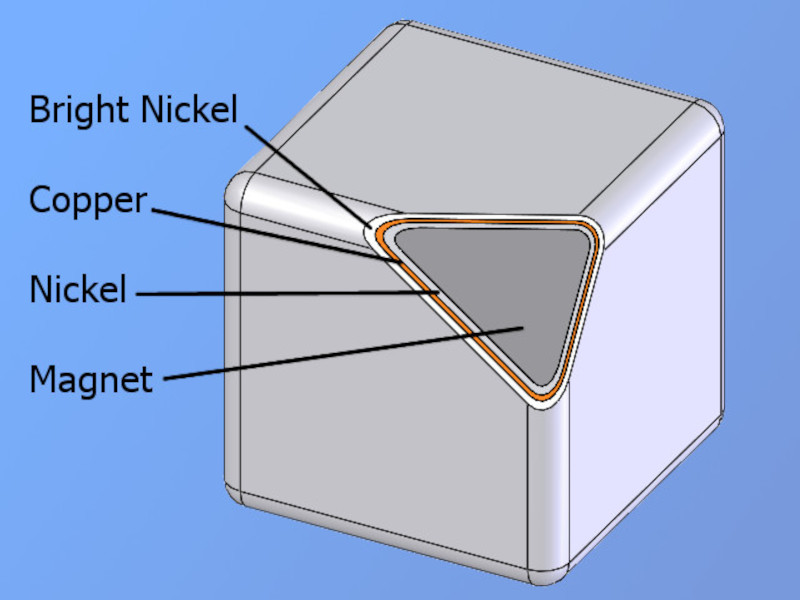
The inside layer of nickel plating is different than the bright nickel above it. The grain structure is different, and no phosphorus is used in the plating process. These differences mean they sit in slightly different positions on the galvanic corrosion chart. The top nickel layer will typically corrode first, acting in a sacrificial way to protect the underlying layer. Corrosion tends to propagate horizontally across the layer, rather than boring down into the magnet. It's like how a boat's zinc corrodes sacrificially, before the bronze or aluminum propeller.
The copper layer shares this galvanic protection idea, but also helps in other ways. Copper plating forms a ductile underlay that provides some leveling of the rough surface. It's a good choice for materials that are harder to bond to, such as the rough surface of a neodymium magnet.
To learn more about neodymium magnet structure, visit our How Neodymium Magnets are Made article.
2. Testing magnets in harsh environments
Salt water effects on magnets
Over the years, we've heard many anecdotal stories about what works and what doesn't in wet applications. Epoxy coating helps some folks, while others say the nickel plating alone is better. While all these stories hold some truth, we always prefer data that's testable. Today we're sharing an informal corrosion test experiment for magnets in water we started a few months ago.
We submerged some nickel plated magnets, gold plated magnets and epoxy coated magnets into salt water. We scratched one of each type with a knife, and left a second unscratched. What happened over time?
Test results for salt water exposure
Only one DC2E epoxy coated magnet survived the 6-7 weeks of salt water submersion. Does that mean using epoxy is OK? No, not really. Our sample size is very small. Also, the scratched epoxy magnet started rusting at the edge, in a completely different location than the scratch. If we conducted this same test on 100 epoxy coated magnets, we suspect some percentage would fail.
There also wasn't a clear answer on how long it takes before corrosion sets in, despite the identical conditions. The first magnet to fail showed a rust bubble after about 1 week. The last magnet to rust didn't start showing problems until after a month!
In previous testing, gold plated magnets lasted longer than nickel plated, but that certainly wasn't true here. The only sure conclusion is that corrosion is coming, though it is hard to predict when.
We measured these 6 test magnets before and after corrosion testing. Careful measurements with a fluxmeter noted the total magnetic moment of each magnet.
After the testing, we found decreases in strength ranging from 0% to 11%. The epoxy magnet with no visible rust tested just fine. The gold plated magnet with the most rust, pictured above, was the weakest. There is simply less non-rusted magnet material available.
Testing effects of outdoor exposure to magnets
We love this kind of down to earth, hands-on testing. For example, we've stuck a number of magnets outside for years, monitoring how corrosion progresses in the sun and rain. It's an informal test outside of our regular qualification testing, but still interesting. Here are a few examples:
-
Stainless steel mounting magnet A few of our stainless steel magnets have been outside since late 2013, and still show no signs of rust! We never expected them to hold up this long. Expectations exceeded!
-
Rubber coated ring magnet A single, natural rubber coated ring magnet has not fared well in the sun and rain. Cracks in the rubber has allowed extensive corrosion of the magnet. It still sticks, but the magnet is no longer a complete ring.
Again, the cause isn't moisture, but UV exposure in the sun. We no longer carry a natural rubber coating, but have switched to thermoplastic rubber.
-
Thermoplastic covered block magnet This block magnet is coated in a rubber-like thermoplastic, which has held up well so far. It has only been outdoors since late 2018, so time will tell.
-
Black and red plastic coated cylinder magnet Our plastic coated magnets have an injection molded layer of plastic. The plastic forms a waterproof shell around the magnet. While the magnet inside has remained free of moisture and rust (see video for a peel-away of the plastic), it has faded in color. The rust in the phot is from the steel door and not the magnet. The plastic feels more brittle than new magnets, thanks to exposure to the sun's UV rays. These examples have been outdoors since late 2016, about three and a half years.
Testing magnets in saltwater, bleach and vinegar
More recently, we tested our thermoplastic rubber coated magnets plastic and in three different solutions: saltwater, a bleach cleaning solution, and a vinegar solution. After 5 months, the only corrosion was found in the thermoplastic rubber vs vinegar solution. All others passed with flying colors! See the video below:
Shop Waterproof Magnets
Check out our selection of plastic and rubber magnet coatings that prevent rust and corrosion.



3. The effects of rust on a magnet
Can rust weaken magnets?
Rust does weaken magnets. When a magnet rusts, it goes through oxidation and forms iron-oxide . Iron-oxide aka rust is not magnetic, and since the actual magnet becomes smaller, it becomes weaker as well. Rust buildup can also create a larger gap between the magnet and what it is attracting to which will lower pull force.
As a result of the above testing, we also observed up to an 11% strength loss in magnets showing signs of rust. Strength loss can differ depending on where and how much of the magnet has corroded.
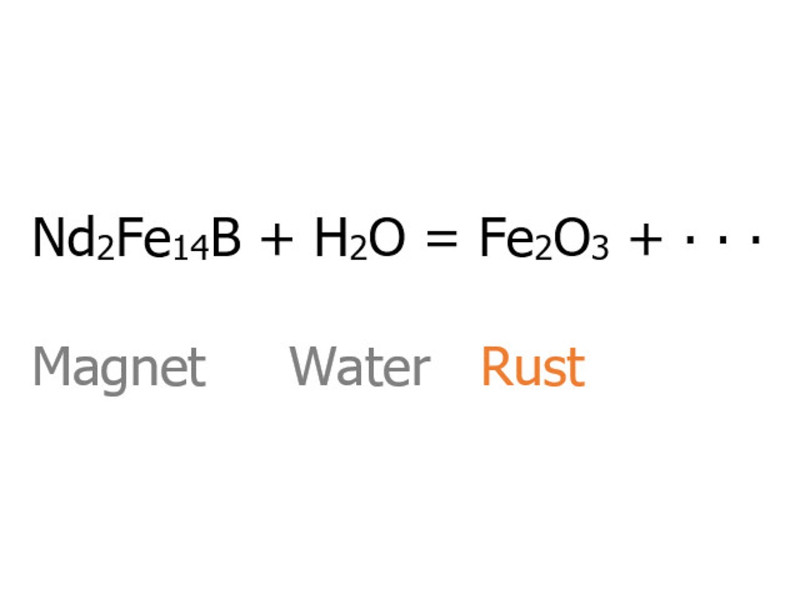
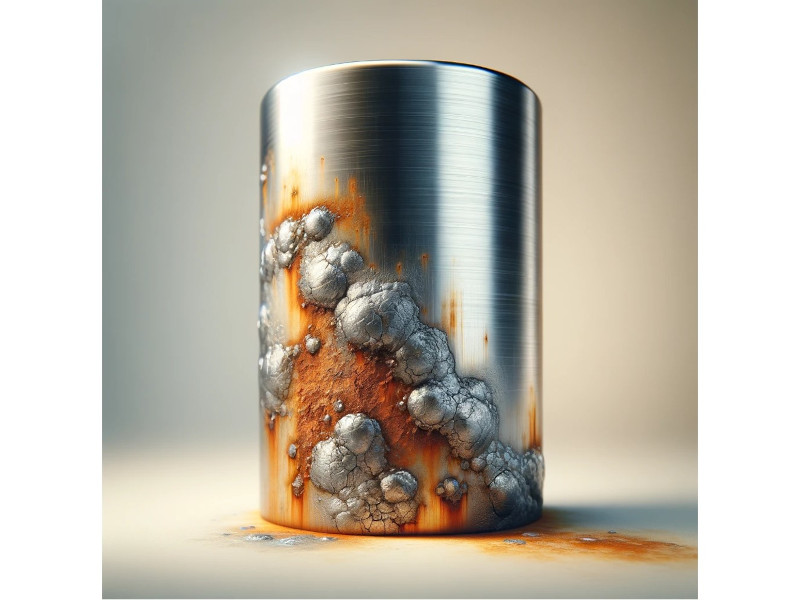
4. How to waterproof a magnet
You can waterproof a magnet by adding a coating that does not react with water such as different types of plastics, rubbers and stainless steel. While neodymium magnets contains iron and will never be rust proof, they will be protected as long as the waterproof layer is intact.
What if I already have a magnet I need to waterproof?
If you already have a magnet and want to coat it in plastic or rubber can check out our How to Rubber Coat Your Own Magnets article for a full DIY guide for magnet waterproofing.
Best waterproof magnets
- Plastic coated magnets: Plastic coated magnets are a great way to add waterproofing to your magnets and can be safely used in many environments, including as aquarium magnets. Learn more about benefits of plastic coatings in our Benefits of Plastic & Rubber Coated Magnets article.
- Rubber coated magnets: A rubber coated magnet not only provides a waterproof layer, but also gives the magnet strong grip strength for hanging. Check out our Leverage & Friction When Using Magnets article for more details.
- Stainless steel mounting magnets: Our stainless steel mounting magnets have a steel cup to protect the back and sides of the magnet and a stainless steel layer to protect the front north face of the magnet.
- Sewing magnets: Our sewing magnets that come inside of a plastic sheath are waterproof and good if they accidentally get run through the washer or the clothes get wet in the rain etc.
Top 7 ways to create corrosion and rust resistance magnets
What if I cannot waterproof my magnets? Even if you cannot use a plastic or rubber magnet in your application, there are still ways to limit the rusting and corrosion of your magnets. Below is a list of 7 ways to help protect your magnets from water and moisture.
- Add coating: We offer a variety of magnet plating and coating options. Although our standard nickel plating is not rust proof, it helps prevent the buildup of rust greatly over a non-coated magnet.
- Protect in sleeve: If you are willing to sacrifice a bit of magnet strength, you can protect the magnet in a plastic sleeve similar to our sewing magnets.
- Use in assembly: Using magnets inside of an assembly can prevent moisture from reaching the magnet, or at least limit the surface area exposed.
- Avoid humidity: Exposure to high levels or frequent humidity can cause rust so try to place in areas with low humidity and no direct contact with water.
- Avoid direct sunlight: UV rays can degrade the coating of magnets, including waterproof plastic and rubber coatings. The material can dry out and crack over time allowing moisture in.
- Avoid high heat: While neodymium magnets have decent heat resistance, they can lose part or all of their strength if they get too hot. Check out our Temperature and Neodymium Magnets article for more info.
- Inspection: Inspecting a magnet before putting it into a harsh environment can identify possible defects in the coating that may accelerate rust and corrosion. Periodic checks can also catch rust starting to form before it becomes a major issue.