What Magnet Coating Should I Use?
Not all coatings are created equal. Find the best magnet coating for your application.
1. Why are magnets coated?
Neodymium magnets are coated or plated for a variety of reasons. The exact reasons will depend on how the magnet will be used. Rubber may be great for grip strength and hanging things, but a colorful plastic magnet for your fridge or a nickel plating finish may be the best options in different situations.
Top 10 reasons neodymium magnets have a coating:
-
Corrosion Resistance: Neodymium magnets are composed of neodymium, iron, and boron (NdFeB). Iron in the alloy makes them susceptible to corrosion, especially in humid environments. A coating provides a protective barrier, preventing the iron from oxidizing (rusting). Check out our Can Magnets Rust? article for more details.
-
Increased Durability: Without a coating, neodymium magnets are relatively brittle and prone to chipping and cracking. A plastic or rubber coating helps protect the magnet from physical damage during handling and use.
-
Enhanced Aesthetics: Coatings can give neodymium magnets a more appealing look, which is important in consumer applications where the appearance of the magnet is a consideration.
-
Health: Some coatings can be allergenic to certain individuals and coatings like gold can help reduce or eliminate symptoms from direct contact with the magnet coating.
-
Improved Functional Performance: Coatings can be used to modify the surface properties of the magnet for specific applications. For example, a rubber coating can provide a non-slip surface, and some coatings may be non-conductive, which is important in certain electrical applications.
-
Cleaning Ability: Certain coatings like epoxy or plastic make neodymium magnets easier to clean and maintain, especially in environments where cleanliness is crucial, such as in kitchens or medical equipment.
-
Electrical Conductivity: Some coatings, particularly metallic ones, can affect the electrical conductivity of the magnet. Non-conductive coatings like rubber or plastic are useful in applications where electrical insulation is necessary.
-
Reactivity: Coatings can reduce the magnet's reactivity with other substances, preventing unwanted chemical reactions in environments where the magnet is exposed to aggressive chemicals or reactive substances.
-
Thermal Conductivity: Coatings can be used to alter the thermal conductivity of the magnet, which can be crucial in heat-sensitive applications.
-
Ease of Handling: To provide a better grip and handling experience, reducing the likelihood of dropping or mishandling, which is especially important for small or intricately shaped magnets.
2. Types of coating and platings
We offer a variety of coatings and plating for our magnets, but it may be difficult to know what the differences are and which one is best for your project or use case. Here we will cover the available coatings and some details on each.
Neodymium magnet plating options:
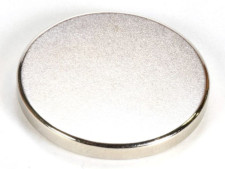
Nickel (Ni-Cu-Ni)
Nickel plated neodymium magnets seem to be the most common and this is the standard for many of our stock magnets as well. Nickel plating is a well-balanced coating that offers various benefits such as: corrosion resistance, a smooth finish, has good adhesion to magnet and is considered non-toxic in many applications.
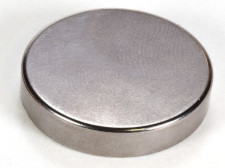
Black nickel plating (Ni-Cu-Ni-BlackNi)
Our black nickel finish performs the same as our standard nickel finish, just with a darker tint on the outside layer of nickel.
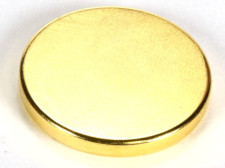
Gold plating (Ni-Cu-Ni + Au)
The gold finish is placed on top of our standard nickel plating and adds another layer of protection in addition to a different aesthetic appeal. A gold plating may best best for anyone that suffers from nickel allergies in relation to magnetic prosthetics or treatment.
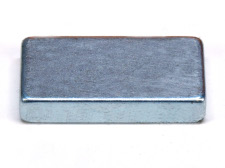
Zinc plating (Zn)
A zinc coating layer can be used in certain applications where a nickel plating will react with a compound and has a similar look to the nickel finish, just with a slight bluish tint to it. It also can have superior bonding strength with steel and iron.
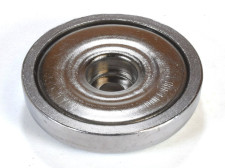
Stainless steel
While this is technically a shell and not a plating, it offers superior rust prevention, water resistance and the steel cup design of the pot magnet provides good shock absorption.
Neodymium magnet coating options:
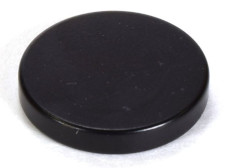
Black epoxy coating (Ni-Cu-Ni + epoxy)
This black epoxy layer sits on top of our base nickel coating and provides a smooth layer and moisture resistance.
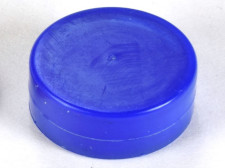
Colored plastic coating (PP)
Our injection molded polypropylene coatings offer a colorful way to protect your magnets from moisture in addition to adding impact absorption and a smooth surface. Great for use in water and aquariums.
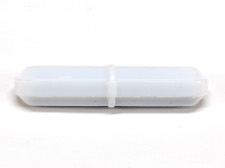
Teflon plastic coating (PTFE)
Our PTFE coating is only available for our magnetic stir bars, but excels at not reacting with many compounds and a top choice for many stir chemistry applications.
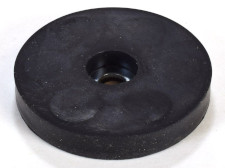
Silicon rubber coating
This is a standard silicon rubber coating and excels in providing high-friction for good traction and hanging. The rubber also provides impact resistance as well as waterproofing.
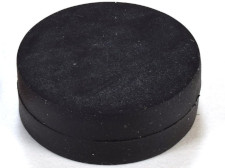
Thermoplastic rubber coating
Our thermoplastic magnets are very similar to our rubber coated magnets, but offer a slightly more durable layer that can stand up better to UV radiation in addition to good traction and water proofing.
Explore Neodymium Magnets



3. Best coatings for neodymium magnets for the 10 most common uses
I think it goes without saying, but there is no single coating or plating for neodymium magnets that is the top performer in every situation. However, there are coatings that are the best for specific uses. Here we will take a look at the best coating or plating for each of several common use cases for neodymium magnets.
-
Normal magnet use
If you will not be using your magnets for hanging and they will not be exposed to moisture or other harsh environments, the standard nickel finish may be best. The black nickel is also great and has a different visual appeal.
-
Impact resistance
Neodymium magnets are brittle by the nature of their manufacturing process and can shatter just from clicking together too hard, falling, or other impact. Many of the standard coatings like the nickel plating help protect against corrosion, but not much against shocks. Our plastic and rubber coatings as well as our steel cup mounting magnet design absorb a lot of shock and help prevent magnets from breaking.
Best impact resistant magnets
-
High heat
While we have not tested the maximum heat tolerance of each type of coating, the metal plating options should fare better in high-temperature applications. In addition to the plating, the magnet heat grade itself must be able to withstand the intense temperature or it may lose strength.
Best magnets for high temperature applications
- High temp magnets
-
We provide high temperature neodymium magnets in the following grades and can provide them as custom magnets if they are not available in a stock part on our website.
Available high temp magnet grades:
- NM
- NH
- NSH
- NUH
- NEH
- NAH
Learn more about how temperature affects neodymium magnets
-
Hanging
Many people expect to get the magnet strength listed for all uses, but when hanging, you can lose a large amount of strength due to low friction. The rubber grommets and pads on our hook magnets are also perfect for hanging.
Best magnets for hanging
Learn more about hanging with magnets
-
Strong grip
If you need magnets that will have good traction on many surfaces and not slide, a rubber coating would be ideal.
Best magnets for a strong grip
Learn more about rubber coatings
-
Attaching magnets to steel
Our mounting magnets are made to attach directly to metal. Their unique steel pot magnet design redirects the south pole flux lines around close to the edge of the north face of the ring and creates a stronger pull force to steel.
Our fishing magnets work the same way and are made to attach directly to ferrous metal objects in rivers and lakes, etc.
Best magnets for attaching to steel
Learn more about magnets on steel
-
Outdoor use
Just because a magnet is waterproof, does not mean it is also best for outdoor use. Many plastics experience UV radiation degradation over time and can dry out. When plastic dries out, it tends to become very brittle and crack, thus exposing the magnet inside directly to water and moisture. Therefore, our plastic, thermoplastic rubber, and stainless steel mounting magnets are best suited as they are both resistant to UV radiation and provide a waterproof barrier to protect the magnets from rusting.
Best magnets for extended outdoor use
How you can use magnets outdoors
-
Wet and moist environments
The best magnet coatings for high exposure to humidity and water are any of our plastic and rubber coated magnets, our stainless steel mounting magnets or our plastic cover sewing magnets. All of these coatings provide a waterproof layer to protect the magnet inside from rust and corrosion.
Best magnets for water and moisture exposure
-
Aquariums
There are many types of waterproof coatings for magnets, but not all of them are reef and aquarium safe. Certain compounds in fresh and salt water fish tanks can react with the magnet coating and chemicals can leach out into the water. In an aquarium or reef setting, our plastic coated magnets are a safe option.
Best reef and aquarium safe magnets
Learn more about using plastic magnets in aquariums:
-
Lab testing with magnetic stir bars
Many labs prefer to use a Teflon (PTFE) coating on their magnets in stir bar chemistry. This involves using a magnet to mix different chemicals. PTFE excels here as its strong covalent bonds make it less reactive to many chemicals.
Best magnets for stir bar chemistry
Learn more about stir bar chemistry: